Garage Floor Chandler AZ can be cost-effective, rewarding, and relatively straightforward, depending on the chosen flooring material and the homeowner’s level of skill and experience.
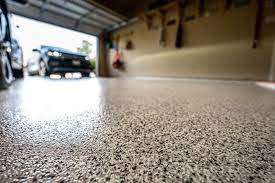
Here are some popular DIY options for garage floor installation:
1. Epoxy Coatings: Epoxy garage floor coatings are a popular choice for DIY installations due to their ease of application, durability, and aesthetic appeal. Epoxy coatings typically come in two parts – a resin and a hardener – that are mixed together before application. Homeowners can apply the epoxy coating using a roller or squeegee, following the manufacturer’s instructions for mixing, application techniques, and curing times. Epoxy coatings create a seamless, high-gloss surface that is resistant to stains, impacts, and chemicals, making them ideal for garage environments.
2. Interlocking Garage Floor Tiles: Interlocking garage floor tiles are another DIY-friendly option that provides a quick and easy way to upgrade the garage floor. These tiles simply snap together like puzzle pieces, creating a uniform surface that is resistant to stains, impacts, and chemicals. Interlocking tiles come in various materials, including PVC, polypropylene, and rubber, and are available in a wide range of colors, patterns, and styles. Homeowners can install interlocking tiles themselves using basic hand tools, such as a rubber mallet or hammer, and following the manufacturer’s instructions for layout and installation.
3. Rubber Mats: Rubber garage floor mats are a simple and cost-effective DIY option for covering the garage floor. These mats provide a durable and resilient surface that helps protect the underlying concrete from damage caused by heavy equipment and vehicles. Rubber mats come in various thicknesses and styles, including solid mats, perforated mats, and anti-fatigue mats, and can be easily trimmed to fit the dimensions of the garage floor. Homeowners can install rubber mats themselves by simply rolling them out and securing them in place with double-sided tape or adhesive.
4. Concrete Stain: Concrete stain is a DIY-friendly option for enhancing the appearance of existing concrete garage floors. Stains penetrate the concrete surface to create a permanent color that won’t peel or fade over time. Homeowners can choose from a wide range of colors and application techniques to achieve custom designs and effects. Applying concrete stain typically involves cleaning the floor, applying the stain with a brush or sprayer, and sealing the surface with a protective sealer. With proper preparation and application, DIY concrete staining can transform a dull concrete floor into a vibrant, attractive surface.
5. Concrete Sealers: Concrete sealers are another DIY option for protecting and enhancing existing concrete garage floors. Sealers penetrate the concrete surface to form a protective barrier against moisture, stains, and chemicals, while also enhancing the appearance of the floor. Homeowners can choose from water-based or solvent-based sealers, as well as clear or tinted formulations, to achieve the desired level of protection and aesthetics. Applying concrete sealer typically involves cleaning the floor, applying the sealer with a roller or sprayer, and allowing it to dry completely before use.
6. Garage Floor Paint: Garage floor paint is a budget-friendly DIY option for covering and protecting concrete garage floors. Epoxy or latex-based paints can be applied directly to the clean, dry surface using a roller or brush, creating a durable and attractive finish. Garage floor paint is available in a variety of colors and finishes, allowing homeowners to customize the look of their garage space. With proper preparation and application, DIY garage floor painting can provide a quick and easy way to refresh the appearance of the floor.
7. Modular Flooring Systems: Modular flooring systems consist of interlocking plastic or PVC tiles that snap together to create a durable and customizable surface for garage floors. These systems are designed for easy DIY installation and can be configured to fit any size or shape of the garage. Modular flooring is resistant to stains, chemicals, and impacts, making it an ideal choice for garage environments. Homeowners can install modular flooring themselves using basic hand tools, such as a rubber mallet or hammer, and following the manufacturer’s instructions for layout and installation.
Conclusion:
Garage Floor Chandler AZ With proper preparation, tools, and techniques, homeowners can achieve professional-quality results and enjoy a clean, attractive, and functional garage floor for years to come.
The Garage Floor Company Arizona
2300 W Pecos Rd #126, Chandler, AZ 85224, United States
1-480-405-1661