Preparing a worksite for Concrete Crew Mesquite TX is a crucial step in ensuring a successful construction project. Proper preparation helps create a stable foundation, ensures accurate placement of concrete, and minimizes the risk of issues such as cracks or uneven surfaces.
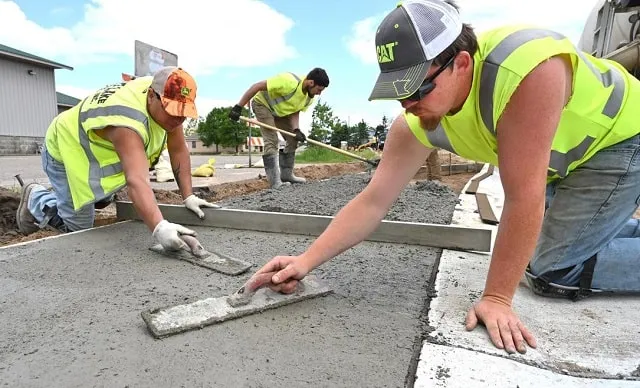
Here are the essential steps in preparing a worksite for concrete pouring:
- Site Assessment and Planning:
- Before starting any work, conduct a thorough assessment of the site to identify potential hazards, obstructions, and soil conditions. Consider factors such as site access, drainage, and proximity to utilities. Develop a detailed plan for the concrete pour, including layout, formwork requirements, and sequencing of activities.
- Site Clearing and Grading:
- Clear the site of any debris, vegetation, or obstructions that could interfere with the concrete pour. Use heavy equipment such as excavators, bulldozers, or skid-steer loaders to grade the site to the desired elevation and slope. Ensure that the ground is compacted and stable to support the weight of the concrete.
- Layout and Marking:
- Mark the boundaries of the concrete slab or structure using string lines, stakes, or spray paint. Use a tape measure and level to ensure accurate dimensions and alignment. Mark the locations of control joints, expansion joints, and any embedded fixtures or anchor bolts as specified in the project plans.
- Formwork Installation:
- Construct formwork, also known as molds or shuttering, to contain and shape the concrete during pouring and curing. Formwork can be made from wood, metal, or plastic, depending on the project requirements. Install formwork according to the layout markings, ensuring proper alignment, bracing, and reinforcement as necessary.
- Reinforcement Placement:
- Install reinforcement materials such as rebar (reinforcing bar) or wire mesh within the formwork to provide strength and structural integrity to the concrete. Position reinforcement according to engineering drawings and specifications, ensuring adequate cover and spacing between bars. Use tie wire or chairs to support and secure reinforcement in place.
- Embedments and Inserts:
- Install any embedded fixtures, anchor bolts, or utility conduits required for the project. Place these items within the formwork, ensuring they are properly positioned and aligned according to the layout markings. Use templates or guides to ensure accurate placement and spacing of embedments.
- Surface Preparation:
- Prepare the subgrade or base surface to ensure proper bonding and adhesion of the concrete. Remove any loose material, dirt, or debris from the surface. Compact the subgrade using a compactor or roller to achieve a firm, uniform surface. Apply a layer of granular fill or gravel to improve drainage and prevent soil erosion.
- Moisture Management:
- Manage moisture levels in the subgrade and formwork to prevent issues such as excessive drying or water accumulation. Use moisture barriers or vapor barriers as necessary to control moisture migration from the subgrade. Avoid pouring concrete in wet or rainy conditions that could affect the quality of the finished product.
- Joint Preparation:
- Prepare control joints, expansion joints, and construction joints as required to control cracking and accommodate movement in the concrete. Install joint filler materials or preformed joint strips to protect joints from debris and facilitate movement during curing. Ensure that joints are properly spaced and aligned according to project specifications.
- Final Inspection and Approval:
- Conduct a final inspection of the worksite to ensure that all preparations have been completed according to the project plans and specifications. Verify the alignment, dimensions, and condition of formwork, reinforcement, and embedments. Address any issues or discrepancies identified during the inspection before proceeding with the concrete pour.
By following these essential steps, a Concrete Crew Mesquite TX can effectively prepare a worksite for concrete pouring, laying the foundation for a successful construction project. Proper preparation ensures that the concrete will be placed accurately, bonded securely, and cured to achieve the desired strength and durability.
Mesquite Concrete Crew
109 Rollingwood Dr, Mesquite, TX 75149, United States
1-972-848-9594